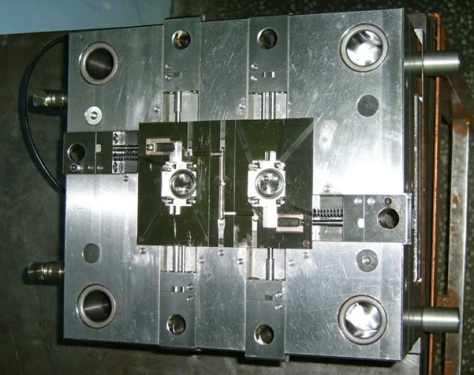
Clinching Screw,Stainless Steel Screws,Brass Screws,Sheet Metal Screws,Pan Head Screw
Dongguan Tiloo Industrial Co., Ltd , https://www.sales-fastener.com
Clinching Screw,Stainless Steel Screws,Brass Screws,Sheet Metal Screws,Pan Head Screw
Dongguan Tiloo Industrial Co., Ltd , https://www.sales-fastener.com