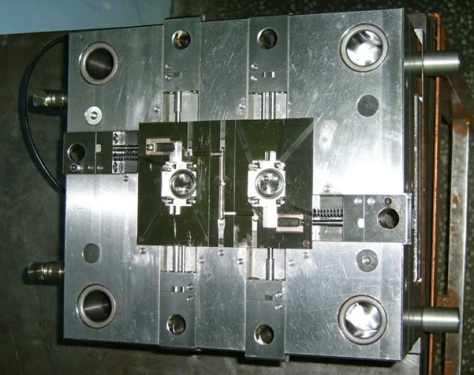
Clinching Nut,Hex Rivet Nut,Self Clinching Rivet Nut,Rivet Nuts Screwfix,Rivet Nut
Dongguan Tiloo Industrial Co., Ltd , https://www.sales-fastener.com
Clinching Nut,Hex Rivet Nut,Self Clinching Rivet Nut,Rivet Nuts Screwfix,Rivet Nut
Dongguan Tiloo Industrial Co., Ltd , https://www.sales-fastener.com