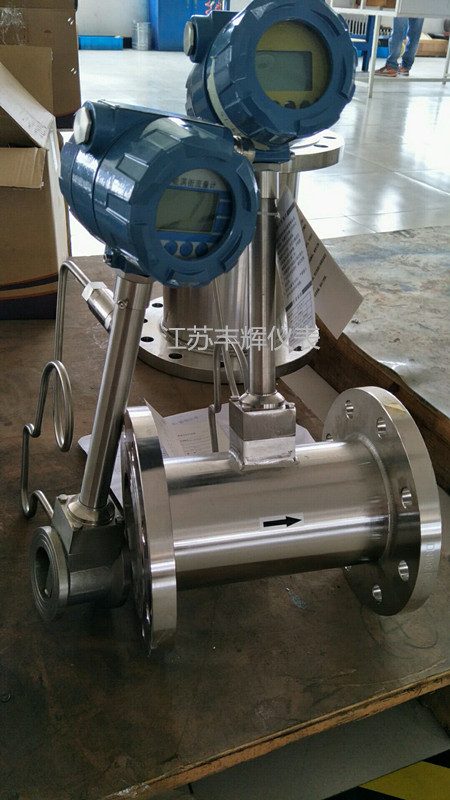
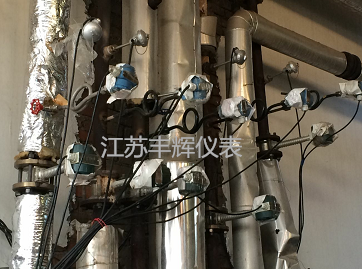
Fault phenomenon
Possible causes and treatment methods
After the power is turned on, the flowmeter has no zero (4mA) output.
The positive and negative poles of the power cord are reversed. Should be reconnected.
The power supply voltage is wrong. Check the voltage on the flowmeter terminal should be in the (17 ~ 30) V range.
Secondary table lead line failure. Check the line.
When there is flow, the flow meter has no output current.
Pipeline flow is less than the lower flow rate that the flowmeter can detect. Change the pipe diameter and increase the flow rate.
The gain of the amplifier board is insufficient or the trigger sensitivity is too low, adjustable K1 or K2.
Poor contact between the amplifying plate and the coefficient plate. Clean the connection points, reload the coefficient plate, and tighten the stud nut.
Instrument circuit failure, find out the faulty part of the circuit for repair.
There is no flow in the pipe, but the flowmeter has a signal output.
Zero bias. Zero (4mA).
The pipe vibration is intense, causing the instrument to have an output signal. Reinforce pipes and reduce vibration.
Trigger sensitivity is too high. Adjustable K2, so that the TP3 output just disappears, the pointer on the scene pointer back to 0%.
Instrument circuit failure, find out the faulty part of the circuit for repair.
Flowmeter output signal is not stable, the pointer swings too much.
Process flow is at the critical point of the meter's lower flow point. Adjustable K2 and damper switch for stable output.
Poor contact of the circuit or leads, check contact points.
When the flow rate increases, the output current does not go up.
The load resistance of the flowmeter is too large. Reduce the load, or increase the power supply voltage, up to 30V.
circuit failure. According to Section 7 method inspection.
The flow shows a large deviation.
The flow meter setting range (Qmax) and the secondary instrument set range are not correct. Re-adjust the secondary meter range.
Flowmeter transformation factor KB calculation error. Recalculate KB and select J.
The design conditions are different from the actual conditions. Recalculate KB and J coefficients according to actual conditions and readjust them.
The wrong position of the KB encoder switch or the incorrect position of the J connector. Re-adjust the switch, connector.
Circuit failure, maintenance.
Â
Silicone glove/mitt,High Quality Silicone glove/mitt,Silicone glove/mitt Details, CN
Yangjiang YJCB Trade Co., Ltd , https://www.cbprokitchen.com