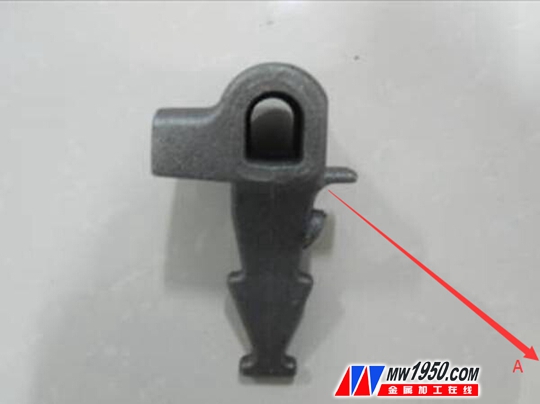
Slag inclusion
Daoming Reflective Fabric use different resin, put the hi- reflective index`s glass bread on the base fabric well distributed. Behind all the glass bread has reflective layer coating. When the light was on the surface,glass bread made light source to reflected light beam. The light passes through the incident - refraction - reflection process, showing bright light, forming a retroreflective function.Personal safety reflective fabric applied to fashion, shoes,hat,suitcase, sports, casual, decoration,security, advertisement and etc. Varies of product could meet customer`s customize.The application scene covered almost all the reflective field.
Our product conforms to EN471,australia standard AS/NZS4602 ,OEKO-TEX100 and ANSI107-1991
Reflective Fabric
Reflective Fabric,TC Reflective Fabric,Silver TC Reflective Fabric,Gray TC Reflective Fabric
Daoming Optics & Chemical Co., Ltd , http://www.dmreflective.com