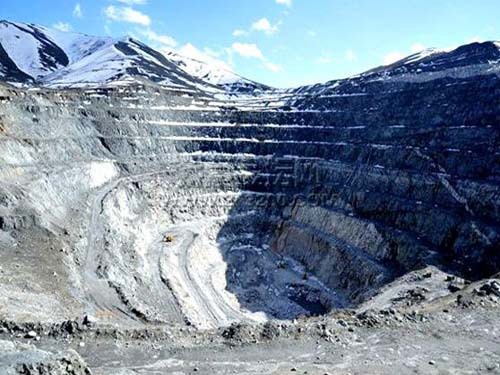
Using revolutionary digital and technological innovations, the mining industry may be able to make breakthroughs. In this article, we will elaborate on several digital technologies. There has long been research to analyze these technologies, and today these technologies are finally cheap enough to be used on a large scale in the mining industry. Their application scope includes a more comprehensive understanding of basic resources, optimization of raw materials and equipment processes, enhancement of fault prevention work, enhanced mechanized automation, and real-time monitoring of performance.
Individually, each condition has enough potential. And their combination means a fundamental shift in potential security and capture of mining value. We will outline these opportunities and come up with a number of key issues that are worthy of attention by the miners.
It is imperative to increase productivity
The analysis shows that the global mine productivity has decreased at a rate of 3.5% per year over the past 10 years. This trend is evident in many types of subdivided products, regions, and most mining companies. Although people have been arguing over the causes of their decline, a consensus has been reached on this point: As the outlook for the industry has deteriorated, most mining companies have shelved or cut their expansion plans, and even rethink whether they should expand or shrink their businesses. As a result, productivity in the mining industry tends to be flat, and even in some areas or on certain commodities, productivity has begun to recover.
But there is clearly room for productivity growth. One way to quantify this potential is to compare the mining industry with other industries such as upstream oil, natural gas, steel, and oil refining. Using the benchmark we set as a reference, it can be observed that the average global equipment efficiency (OEE) for underground mining, surface mining, and comminution grinding is 27%, 39%, and 69%, respectively, across the world. In contrast, the OEE of upstream oil and gas is as high as 88%, steel is 90%, and oil refining is 92%.
Of course, the mining industry has many differences with other industries. Its uncertainty is quite high and the assessment of the exploitability of resources from the very beginning is full of variables. Mining environments are often extremely harsh and remotely located. Not only that, but just transporting workers to the mining site (whether it is the arrival of air transport personnel into the mine, the transport of personnel into the ground or the return to the ground), it has consumed a lot of valuable time. In addition, due to the unpredictability of ore size and hardness, mining equipment is constantly subjected to excessive pressure, resulting in a collapse accident.
But this is the key. To reduce external pressure, intelligent planning and coordination of activities are essential. The strict discipline can eliminate the uncertainty caused by the miners themselves. By reducing or even eliminating as much as possible mining-specific risks, the mine's productivity will rise by a further step.
The turning point in the mining industry
We believe that the mining industry is at a turning point. At this time, digital technology may bring new ideas for uncertainty control and productivity improvement. The trend of large-scale use of the following four cluster technologies has become increasingly significant.
Data, computing power and connectivity
By embedding a large number of sensors in real objects, people can not only obtain large amounts of data for analysis, but also enable communication between machines. And the cost of this technology has become cheaper and more feasible; smart grids can report on the electricity usage of millions of homes; when problems arise, sensors on deep-sea wells will send warning signals to the control center. In 2015, more data were generated each day than in the year of 2003. The mining industry has been able to obtain large amounts of data. Their understanding of the mines is more precise and continuous than before.
Analysis and Intelligence
In order to better integrate data, the machine will "learn" to improve statistical techniques. Thanks to advanced analytical capabilities, people can use massive data sets to predict the probability of future events. Complex mining tasks, such as geological modeling, scheduling, and maintenance forecasts, will play an important role in the application of intelligent statistics and optimization algorithms.
Human-machine dialogue
Smartphones and other mobile devices have allowed human interaction objects to expand from the same category to machines. Consumers have been inseparable from smart phones in terms of navigation, booking of taxis, and monitoring of health conditions. The popularity of smart devices in the industrial field is rapidly increasing. Smart glasses are a typical example. Smart glasses can provide guidelines for production line workers, or instruct them to repair faulty equipment and enhance operational discipline. Another example is workwear with sensors. Such work clothes enable managers to obtain data on the related hazards and the physical condition of workers in order to improve work safety.
Digital-to-physical conversion
We have made some progress in the field of robotics, and now we can produce cheaper, more efficient fully automated equipment. In the manufacturing industry, the cost of industrial robots has dropped by 50% since 1990, while the American labor price has risen by 80% during the same period. At the same time, with the technological advancement in areas such as artificial intelligence, robots have a wider range of applications. In mining, equipment for telecommunications and auxiliary control equipment is becoming more and more common. In addition, people have introduced fully automatic equipment to carry out traction, drilling and other work.
In summary, these technologies can fundamentally change the way minerals are operated. This change is not only reflected in the use of information flow to reduce the risk of decision-making, but also reflected in the adoption of more centralized and mechanized operating methods to reduce operational risks.
Future performance
Our view is that when these technologies are embedded in the mining industry chain as a whole, their maximum value will be realized. Next we will analyze what kind of value bodies it can create.
Basic understanding of resources
There is almost no problem that can stimulate the nerves of mining executives: If you can accurately know the composition and location of underground ore, what will happen? In the past, from the exploration to the short-term mining plans, the process of excavating resources was often divided into several small links by organizational boundaries, data sources, and geological models. But now, miners can better understand resources through on-line sampling, combined with ore body model information and drillhole data.
The statistical techniques of integrating mining data can increase the probability of discovering ore and deepen the depth of drilling of the target in order to maximize information gains. People combine geological information with better and more universal laws to optimize drilling and blasting patterns, create an executable mine plan, and kill quality problems in the cradle.
Material and equipment flow optimization
In essence, the mining supply chain is an interactive system of multiple fixed and mobile devices. Tools and indicators such as OEE are the basis for business improvement, but they cannot master the complexity of the system. Real-time data and better analysis projects speed up the scheduling and equipment and land use. For example, in mines, combining traditional scheduling and intelligent algorithms can maximize efficiency. Another example is that in the processing plant, many plant operators have blind spots in their understanding of the drivers of production. New mathematics techniques can find hidden relations between second-order and third-order variables to solve this problem. We have found that factories using this technology have increased the production of gold, nickel, phosphate and other minerals by 3 to 10 percentage points.
Improve forecasting
Mineral companies have a tradition of collecting large numbers of drill bits, trucks, processing plants, and train data. However, these data have not been fully utilized. In some cases, the mining company's utilization of information is only 1% or even less. Using this information can calculate the probability that a particular part will fail, instead of relying on traditional time calculations to reduce maintenance costs and prevent accidents.
Improve machinery automation
Automation can reduce operating costs, enhance operational discipline, and protect the personal safety of staff. Some technologies, especially automated transportation and drilling, have achieved large-scale commercialization. Other technologies, especially automatic blasting and eradication, are still in the experimental stage. Our analysis believes that the economic benefits brought by transport automation are enormous - the total cost of ownership will be reduced by 15% to 40%. The specific rate of decline depends on labor costs, because the design of the pit configuration, equipment configuration, and operational transition must be personally determined by the staff. In addition, we believe that mining automation can reduce labor in half of the most dangerous mines.
Real-time performance monitoring
One of the advantages of real-time data is that, in the mining process, people can grasp the situation and specific location of the equipment every second, and in particular, confirm whether the project is proceeding as planned. The real-time management and control technology gives the operation management a new layer of meaning, so that the operation management is no longer just to establish the monthly goal, but to pay attention to changes in the situation and the implementation of the plan. In addition, the real-time data and operation center not only enables immediate feedback, but also makes operations center decisions more thorough. In this way, the center can maximize the value of the whole industry chain, not a subdivision. This kind of performance can be used to monitor accidents on the one hand to improve security; on the other hand, it can ensure high utilization of equipment while reducing the implementation cost of the plan.
Each condition seems to be easy to implement, but only when used together as a whole can they be of the greatest value. There are three reasons why this argument can be explained.
First, the physical technologies required for automation provide real-time information flow, which is the basis for people to better understand the situation. The investment in automation was completed flawlessly. At the same time, people also invested in systems and tools for better decisions.
Second, these decisions will eventually be fed back to fully automated machines, not to human operators. The real value of this closed loop lies in its learning function - continuous decision-making records, working with the machine learning algorithm, will continue to obtain better results from each iteration.
Finally, once a certain part of the system is built on a digital platform, the actual benefits or network effects will extend it to the entire supply chain. The more data a decision algorithm can make, the more efficient it is; the more systematically the operational activities can be recorded, the more valuable these data will be; the wider the range of decision algorithms, the more the operational results will reflect the best business results.
The concept of a fully integrated, automated mining supply chain may not be recognized by the world in the future, but it has long been not confined to the scientific scope of mining - it is the logical end point of a series of technological deployments, and mining companies are nothing more than The initiator only. In addition, it is almost the best choice for mining companies in terms of reducing and controlling risks. At the same time, it can both enhance personnel safety and ensure productivity. Therefore, we think it is an inevitable goal. The question is how long it will take for us to reach our destination.
start sailing
Catching the value of digital innovation represents a fundamental shift in the concept, strategy, operating model, and performance of the mining industry. In particular, it is worth noting that the emphasis of the value creation evaluation of the mining industry will not be material transport, but how to collect, analyze, and increase output based on information. This is a difficult transition, and the transformation of a mining company can only be successful if industry leaders think the prospects for this change are attractive. Our analysis shows that the benefits of this opportunity are considerable - in the year 2025, it will bring about 370 billion U.S. dollars in economic benefits. This amount is about 17% of the global mining costs in 2025.
The key to releasing value is that people regard innovation as an action covering all aspects of business, not just a technical effort. In fact, many technical problems have been broken. For the next generation of mining industry leaders, whether to seize this opportunity is the real challenge.
Technology is its own terminator or rooted in value creation
Mining companies must resist temptation and cannot blindly pursue intelligence at the expense of value. It is not easy to establish a system that can integrate business problems and technology applications. The trick to success is to have a team that knows mining operation technology and understands the integration of new technologies.
Technology is a bigger and better tool in the future or a fundamental change in operating model
If you simply use technology as a new generation tool to reduce direct counting, companies may miss the opportunity to integrate real-time data and decisions. From the center plan to the actual operation site, from the mine to the full-scale operation of the port, the integration of data and decision-making tasks means that the staff will play the role of system engineer, rather than mud porters.
People's transformation will be more efficient
Through our cross-industry big data research, we believe that technology – data, analysis and systems are only part of the answer, and that changes in processes and people are indispensable. Only in this way can technology and methods be used effectively. Successful miners will look at data, look at systems, see core processes, and even look at human capabilities in a holistic way. They are conscious that only when people change their way of working and making decisions can new technologies generate value.
In the initial stage, how will the management effect be?
Earnings are a priority, followed by value development and the ability to extract value from technology. At the same time, a large number of mining companies need to change their traditional control systems, IT systems and data systems in order to implement new technologies on a large scale.
How will the situation adapt?
Many mining companies often do not have clear and innovative managers. Not only that, if only by virtue of existing capabilities, or using the current scorecard, indicators and calculations to capture new opportunities, it seems that only companies will continue the status quo. To achieve this change, the mining company must clearly identify the executives responsible for innovation, redefine the role of a skilled executive, and redesign the plan to create room for innovation.
From mining resources to equipment pressure to weather, the mining industry is always labeled with uncertainty and variability. These factors are the core of the operation of the company. To win in the new era of the mining industry, the key lies in whether the company can clearly realize that this era will finally come. Specifically, with the right investment, companies can reduce or even eliminate uncertainty. With the development of the times, the miners will become a profession that requires knowledge. Although the problems they face remain the same, the solutions are quite different. Companies that are now aware of this change and who have taken the lead in successful transformation will be the future king.
Ultrasonic Remote Water Meters
Ultrasonic Remote Water Meters,Ultrasonic Water Flow Meter,Bulk Water Meters Ultrasonic,Ultrasonic Water Meters Bulk
Ningbo Safewell Plumbing Co., Ltd. , https://www.safewellbrass.com